The nonwoven industry is at a turning point, driven by consumer demands and regulations. Every decision-maker is looking for cost-effective ways to deliver improved properties in a sustainable way. This can be achieved with exceptional expertise and advanced pilot infrastructure.
Today, many industries are pressured to find alternatives to replace plastic, increase the use of recycled and biodegradable materials, and reduce water and energy consumption. The same applies to the nonwoven sector, not least due to the disposable nature of many of its products. However, keeping up with the regulations is not enough. To meet the end users’ growing demands and your financial goals in long term within the planet’s boundaries, you need a development partner with the latest knowledge and technology.
Fossil-free wipes with premium performance
Synthetic materials, which rely on fossil raw materials, dominate nonwovens, and synthetic fibers are prevalent in wiping products. Using fossil raw materials in wipes impacts the environment and creates waste.
“We are actively working on innovative solutions to address these issues. Examples include low-density, highly porous absorptive hygiene wipes, all-cellulose nonwovens with high wet strength for wet wipes, and bio-based antimicrobial additives to extend the lifespan of wiping products,” says Taina Kamppuri, Research Team Leader from VTT.
At VTT, bio-based materials can be processed using advanced technologies to create high-quality, plastic-free nonwovens.
Looking ahead, we are exploring novel product concepts such as multi-use, modular, or self-cleaning wipes.
“These innovations have the potential to significantly enhance convenience and hygiene while prioritising sustainability. By focusing on eco-friendly solutions, we aim to reduce environmental impact and promote a more sustainable future.”
Meet your targets with VTT’s world-class infrastructure
VTT’s pilot line infrastructure in Jyväskylä, Finland, enables nonwoven manufacturers to test and validate new materials and processes. Advanced wet-laid, foam-laid and air-laid technologies can process pulp, powders, and short-cut (up to 20 mm) staple fibres of various origins.
The cutting-edge analysis and testing facilities ensure an R&D process that meets the highest quality standards. With us, you can create scalable, energy-efficient, eco-friendly nonwovens that smoothly transition from pilot to industrial production.
“We are also establishing an innovative open-access pilot line for energy-efficient web production in Jyväskylä, which is set to become operational during the second half of 2025. This pilot line will utilise air-laid technology, which offers flexibility in the production of nonwoven fabrics while significantly reducing energy consumption compared to the wet-laid process,” Kamppuri explains.
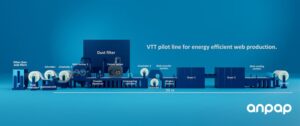
Leverage science to solve your challenges
Our research team combines multidisciplinary knowledge in materials science, process technology and sustainability. This enables us to identify optimal fibre combinations for your specific requirements, develop innovative solutions eliminating the need for synthetic materials and optimise processing parameters to achieve superior product performance.
At VTT, we are innovators by heart, always eager to come up with new ideas and solve customer challenges in ways that no one thought of before. For example, we can enable durable products made from recycled materials, design novel plastic-free hygiene solutions or innovate completely new concepts.
Fast-track your innovation journey
Working with VTT goes beyond accessing advanced facilities and expertise. Our innovation-driven approach helps customers reduce development time and costs through efficient pilot-scale trials, minimizing risks associated with product development.
By partnering with VTT, nonwoven manufacturers can confidently navigate the transition to a plastic-free future. Contact us today to explore how VTT can support your innovation journey.